Обоснование технологической схемы плазменно — химической установки термического обезвреживания пестицидов
В статье изложены результаты изучения технологических процессов при пиролизе пестицидов. Приведены теоретические и экспериментальные данные определения состава отходящих газов. Рассмотрена технологическая схема установки для термического обезвреживания пестицидов и отходящих газов.
УДК 502.174.1
© 2012 г., кандидат технических наук, старший научный сотрудник, эксперт международной ассоциации СОВАСК В.В. Олискевич, кандидат технических наук, доцент С.Ю. Владимиров, кандидат технических наук, доцент И.А.Лобанов, кандидат технических наук Н.Ф.Павлюк, В.В.Чучина, Н.М.Талаловская, заслуженный деятель науки РФ, доктор медицинских наук, профессор, действительный член АВН Н.М.Трошкин
Ключевые слова: отходящие газы, пестициды, термическое разложение, материальный и энергетический балансы, химический состав.
В последние годы в Российской Федерации сложилась неблагоприятная экологическая обстановка в области обеспечения химической безопасности, связанная с накоплением, размещением и утилизацией пестицидов [1]. Это обусловлено плохими условиями хранения пестицидов, их высокой токсичностью для человека, животных и растений, а так же их способностью загрязнять атмосферный воздух, питьевую воду, почву, продукты питания и пищевое сырьё. Ситуация усугубляется тем, что разработанные технологии утилизации отходов производства и потребления не могут быть безоговорочно использованы для решения специфических задач по детоксикации и уничтожению некондиционных пестицидов без угроз экологической безопасности. Поэтому поиск технологических решений обезвреживания пестицидов является актуальным научно-практическим направлением развития современной химической технологии [2,3].
Известно, что наиболее рациональным способом уничтожения промышленных и бытовых отходов является разложение при высокой температуре [4]. В настоящее время термическая деструкция хлорсодержащих пестицидов является одним из экологически ориентированных способов их обезвреживания, в котором химическим превращениям подвергаются как действующее вещество, так и вспомогательные компоненты рецептур [5]. Установлено, что в результате пиролиза количество шлаков хлорсодержащих пестицидов не превышает 30% от исходной массы пестицидов. Их индекс токсичности после пиролиза составляет 3,46, что соответствует третьему классу опасности (умеренно опасные вещества). В итоге при полноте выгорания хлорсодержащих пестицидов не менее 99,97 % в полученной газовой фазе практически не содержится опасных веществ, так как их концентрация не превышает ПДК в воздухе рабочей зоны [6]. Образующиеся зольные остатки и твёрдая фаза в основном состоят из сплавленных силикатов и карбонатов.
Согласно литературным данным [5-8] при термическом разложении хлорсодержащих пестицидов в состав газовой фазы входили такие химические вещества, как: Cl2, HCl, CO, CxHy, CxHyClz и диоксиноподобные соединения. В шлаках и зольных остатках определены CuO, ZnO, PbO, KCl, Na2CO3, CaCO3 и SiO.
Целью настоящего исследования является изучение и разработка технологических процессов обезвреживания непригодных к применению пестицидов. Для исследования были выбраны рецептурные формы хлорсодержащих, азотсодержащих, серосодержащих, фосфорсодержащих, фторсодержащих и металлсодержащих пестицидов в твердом (порошкообразном) виде, в которых действующее вещество составляло от 2,5% до 85% от общей массы в количественном выражении.
Для теоретического обоснования состава отходящих газов при термическом разложении пестицидов использовался единый подход в составлении уравнения высокотемпературного пиролиза рассматриваемых соединений. Примером данного подхода к определению стехиометрического уравнения пиролиза гексахлорана может служить следующая система уравнений, которая строится на принципе аддитивности всех возможных уравнений высокотемпературного окисления пестицида:
C6H6Cl6 + 3O2 → 6CO + 6HCl, (1)
C6H6Cl6 + 6O2 → 6CO2 + 6HCl, (2)
C6H6Cl6 + 3O2 → 3CO2 + 6HCl + 3C, (3)
2C6H6Cl6 + 9O2 → 12CO + 6Cl2 + 6H2O, (4)
или суммарно:
C6H6Cl6 + 5O2 → CO + 4CO2 + C + 4HCl + Cl2 + H2O, (5)
Аналогично рассмотренному примеру можно представить уравнения высокотемпературного окисления и других пестицидов. Исходя из установленных химических реакций термического окисления пестицидов можно предположить, что в состав отходящих газов будут входить оксиды элементов исходных веществ с различной степенью окисления. При этом, если в исходном веществе присутствуют сера и фосфор, то образуются соответствующие сульфидные соединения [9]. Образование оксида углерода (II) и оксида углерода (IV) определяется наличием «застойных» зон в камере сгорания, что может являться конструктивными особенностями печи. В противоположность этому излишек кислорода в камере сгорания способствует образованию двуокиси азота [10].
Появление галогенов и галогенсодержащих веществ в отходящих газах объясняется тем, что на этапе теоретического определения состава газов не представляется возможным учесть все химические реакции термического окисления пестицидов, особенно протекающих в образующихся зольных остатках.
На основании теоретического материала, полученного при определении состава отходящих газов при термическом обезвреживании пестицидов, с использованием общепринятых методов [11] был составлен материальный баланс процесса пиролиза гексахлорана, альдрина, дихлордифенилтрихлорэтана, прометрина, атразина, нитрофена, поликарбоцина, дазомета, тиурама, метафоса, трефлана и хомецина из количественного расчета: 1,0 кг исходного пестицида в твердом агрегатном состоянии и избыток воздуха, участвующего в термическом окислении, в массовом соотношении ɑ = 1,8 [10]. При этом химические реакции термического окисления в зольных остатках не учитывались. К примеру, рассчитанный материальный баланс термического разложения пестицида дазомета в полной мере подтверждает соответствие «прихода» и «расхода» массы веществ, вступающих в химическую реакцию и продуктов реакции (таблица 1). Аналогичные результаты получены при составлении материального баланса отходящих газов при пиролизе других пестицидов.
Таблица 1 – Материальный баланс процесса термического разложения дазомета
Анализ статей материального баланса позволяет оценить объемы воздуха и отходящих газов при сжигании 1,0 кг пестицида (таблица 2).
Таблица 2 – Результаты оценки необходимого объемного количества воздуха для термического разложения пестицидов.
Классификация пестицидов по химическому составу |
Максимально возможный объем воздуха, нм3, для разложения 1 кг рецептурной формы пестицида |
Максимально возможный объем отходящих газов, нм3, при разложении 1 кг рецептурной формы пестицида |
Хлорсодержащие Азотсодержащие Серосодержащие Фосфорсодержащие Фторсодержащие Металлсодержащие |
4,33 5,77 9,05 1,12 0,57 0,98 |
7,29 8,70 13,10 1,75 1,00 1,85 |
Как следует из таблицы 2, наибольшие значения объемных количеств отходящих газов характерны для серосодержащих пестицидов, а наименьшие значения – для фторсодержащих пестицидов.
Результаты определения материального баланса пиролиза пестицидов и данные таблицы 2 позволяют провести оценочные расчеты количества загрязнителей в отходящих газах (таблица 3).
Таблица 3 – Результаты оценки количества загрязнителей в отходящих газах при термическом разложении пестицидов
Тип загрязнителя, определенный по статьям материального баланса |
Значение концентрации загрязнителя в потоке отходящих газов, г/нм3 |
СО СО2 NО2 NO Сl2 HCl SО2 P2O5 P2S3 HF |
29,3 86,0 36,8 18,6 54,9 45,1 75,4 27,7 29,0 17,9 |
Проведенная оценка состава отходящих газов показывает, что в зависимости от химического состава обезвреживаемых пестицидов наибольшие концентрации в потоке отходящих газов выявлены для оксидов углерода и серы, соединений фосфора и азота. Вместе с тем, по нашему мнению, галогенсодержащие соединения будут образовывать сложные вещества с зольным остатком и в газообразной фазе их количество будет минимальным.
Результаты теоретических исследований свидетельствуют о том, что при высокотермическом разложении пестицидов в составе отходящих газов могут быть выявлены такие химические загрязнители, как СО, СО2, NO, NO2 , Cl2 , HCl, P2O5 , HF, SO2 , P2 S3 , в зависимости от исходного состава пестицида. Материальный баланс термического разложения пестицидов позволяет в дальнейшем определить параметры лабораторной установки и разработать технологическую схему очистки отходящих газов.
Нами экспериментально изучен состав отходящих газов при пиролизе модельного образца № 1, представляющего собой смесь гексахлорана, прометрина, метафоса и трефлана, и модельного образца № 2 (пестицид дазомет). Для расчета энергетического баланса процесса пиролиза пестицидов проведены опыты с модельным образцом № 2. Выбор пестицидов обусловлен тем, что согласно теоретическому материальному балансу их термического обезвреживания (таблица 4), в отходящих газах предполагается наличие загрязнителей окружающей среды, для которых необходима разработка система газоочистки.
Таблица 4 – Теоретический материальный баланс процесса термического обезвреживания смеси пестицидов: гексахлорана, прометрина, метафоса, трефлана (модельный образец № 1)
Нами составлен энергетический баланс термического разложения пестицида дазомет. Статьи энергетического баланса включали составляющие, как по приходу тепла, так и по его расходу. Уравнивая между собой статьи баланса и учитывая, что потери теплоты в окружающую среду составляют 10% от общего количества тепла, было установлено необходимое количество теплоты для сжигания 1 грамма пестицида дазомет, которое оказалось равным 34 кДж.
Для исследований по контролю состава отходящих газов, образующихся в процессе термического обезвреживания пестицидов, была разработана и собрана лабораторная установка термического обезвреживания, схема которой приведена на рисунке 1. Лабораторная установка состоит из кварцевой трубки 3 длиной 480 мм, помещенной в электрическую трубчатую печь 1 (марки СУОЛ-0,15.06/12мр) длиной 130 мм, внутренним диаметром 30 мм, с нихромовой обмоткой, обеспечивающей температуру нагрева 900 – 1000 °С. Регулировка температуры проводилась путем изменения напряжения с помощью лабораторного автотрансформатора типа ЛАТР-1М. Рабочую температуру печи определяли с помощью встроенной в печь термопары типа ТХА (хромель-алюмель) с регистрирующим прибором градуированным милливольтметром с диапазоном измерения от 0 до 1100 °С. Для поглощения загрязняющих веществ из отходящих газов кварцевая трубка соединялась с блоком отбора проб 4. Комплектация и подготовка к работе блока отбора проб производится в зависимости от определяемого компонента. Прокачка воздуха через систему осуществлялась с помощью аспиратора ПУ-4Э 5. Скорость прокачки воздуха определялась встроенным в аспиратор ротаметром.
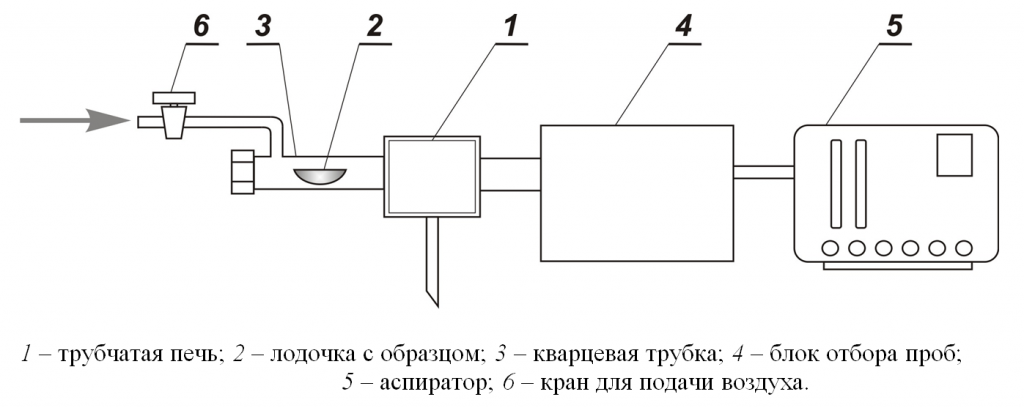
Модельный образец взвешивали с погрешностью не более ± 0, 0002 г. в фарфоровой лодочке, которую вместе с навеской помещают в кварцевую трубку перед входом в трубчатую печь. Трубчатую печь перемещают вдоль кварцевой трубки до попадания фарфоровой лодочки с навеской в центральную, наиболее раскаленную часть печи. Обезвреживание образца проводят при 900 оС в течение 1 часа. Отходящие газы поступают в блок отбора проб. Фарфоровую лодочку с зольным остатком взвешивают и определяют количество образовавшегося зольного остатка. Содержимое блока отбора проб анализируют на содержание компонентов в соответствии с методиками проведения анализов.
Средние значения величин экспериментальных данных по контролю состава отходящих газов, образующихся при пиролизе модельных образцов № 1 и № 2, приведены в таблице 5.
Таблица 5 — Экспериментальные данные по составу отходящих газов, образующихся при термическом обезвреживании модельных образцов
Показатель |
Результаты пиролиза |
Результаты пиролиза |
Тип отходящего газа |
Концентрация, г/л |
Концентрация, г/л |
CO2 |
0,076±0,004 |
0,053 ± 0,001 |
CO |
0,0042± 0,0005 |
0,0042±0,0005 |
NO |
0,0077±0,0008 |
0,0045±0,0004 |
NO2 |
0,019±0,002 |
0,021±0,002 |
SO2 |
0,012±0,002 |
0,038±0,005 |
P2O5 |
0,0043±0,0005 |
— |
HCl |
0,0085±0,0004 |
— |
Cl2 |
0,0015±0,0002 |
— |
HF |
0,0096±0,0007 |
— |
Диоксиноподобные |
— |
— |
Масса модельного образца, г Объем отходящих газов, л Масса зольного остатка, г |
1,0000± 0,0002 4,7 ± 0,1 0,64 ± 0,01 |
1,0001± 0,0002 17,4±0,3 0,179±0,003 |
Анализ полученных теоретических и экспериментальных данных свидетельствует о том, что предполагаемый качественный состав отходящих газов соответствует таковому при экспериментальном термическом обезвреживании модельных образцов пестицидов. Для определения соответствия данных по составу и количеству примесей в отходящих газах, полученных расчетным и экспериментальным путем, составлен материальный баланс процесса термического обезвреживания модельного образца №1 на основе результатов эксперимента (таблица 6).
Таблица 6 – Материальный баланс процесса термического обезвреживания модельного образца № 1, составленный на основе экспериментальных данных
Установлено, что количество газообразных продуктов горения в расчетном и экспериментальном материальных балансах процесса различается. Расхождения по содержанию (массовых долей) загрязнителей отходящих газов по теоретическим и экспериментальным данным составляют от 9,6 до 120,5 % и зависят от типа загрязнителя (таблица 7).
Таблица 7 – Обобщенные экспериментальные данные и результаты теоретических расчетов по содержанию основных загрязнителей отходящих газов
Тип загрязнителя |
Содержание в соответствии с теоретическим материальным балансом |
Содержание в соответствии с экспериментальным материальным балансом |
Расхождение содержания (массовых долей) загрязнителей по теоретическим и экспериментальным данным, % |
||
масса, г |
массовая доля, % |
масса, г |
массовая доля, % |
||
CO |
43,07 |
0,95 |
19,76 |
0,33 |
96,9 |
CO2 |
188,88 |
4,15 |
354,85 |
5,94 |
35,5 |
SO2 |
40,30 |
0,89 |
58,55 |
0,98 |
9,6 |
NO |
35,89 |
0,79 |
35,87 |
0,60 |
27,3 |
NO2 |
87,51 |
1,92 |
87,53 |
1,47 |
26,6 |
P2S3 |
12,67 |
0,28 |
не |
не |
— |
P2O5 |
62,38 |
1,37 |
20,22 |
0,34 |
120,5 |
По нашему мнению, выявленные различия в содержании оксида углерода (II) и оксида углерода (IV) по результатам экспериментального и теоретического материальных балансов объясняются тем, что при термическом разложении происходит окисление оксида углерода (II) и его количественное уменьшение, сопровождающееся увеличением содержания оксида углерода (IV). Отсутствие сульфида фосфора и меньшее содержание оксида фосфора (V) в составе отходящих газов при проведении эксперимента обусловлено, по-видимому, химической реакцией более глубокого окисления фосфора, чем предполагалось при расчете теоретического материального баланса процесса термического обезвреживания образца. Результаты исследований могут служить основанием для разработки системы газоочистки на лабораторной установке термического разложения пестицидов.
Обоснование основных параметров лабораторной установки проводилось в соответствии с понятиями теории синтеза химико-технологических систем (ХТС) [12].
Математической моделью ХТС по очистке отходящих газов является система уравнений технологических связей между блоками (аппаратами) совместно с математическим описанием каждого аппарата данной системы. В каждом аппарате осуществляется некоторое преобразование, которое можно описать следующей функциональной зависимостью [12]:
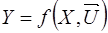
где X и Y – некоторые скалярные величины параметров состояния входных и выходных потоков соответственно;
U – вектор управления указанными потоками.
Таким образом, связи между аппаратами в технологической схеме задаются соотношением [13,14]:
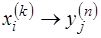
что определяет собой i-ю входную переменную k-го блока конгруэнтно j-ой выходной переменной блока n.
Математическое описание каждого аппарата в технологической схеме имеет вид [15]:

Полная химико-технологическая система газоочистки отходящих газов разрабатывалась на основе следующих трех взаимосвязанных моделей:
- операционно-описательной, указывающей физическую сущность процесса;
- функциональной, использующей блоковый алгоритм описания процесса;
- операторной, использующей тензорное счисление полученного алгоритма.
В рамках операционно-описательной модели исследованы уравнения реакций при термическом обезвреживании исследуемых пестицидов, процессы, происходящие в аппаратах системы, а также сведения о составе сырья и значения параметров технологического режима.
Функциональная модель ХТС разрабатывалась на основе операционно-описательной модели, определяя собой технологические связи между процессами. Функциональная модель позволяет прослеживать последовательность совершения технологических процессов. Данная модель представлена на рисунке 2.

Операторная схема в отличие от функциональной модели дает наглядное представление о физико-химической сущности технологических процессов системы. Для этого каждый элемент ХТС изображают в виде определенного типового технологического оператора, который качественно и (или) количественно преобразует физические параметры входных материальных и энергетических потоков, т.е. совершает операцию.
Операторная схема ХТС основана на том, что каждый элемент ХТС представляет собой совокупность нескольких типов технологических операторов или отдельных типовых технологических операторов.
Если в качестве основных потоков принять объемный (массовый) расход газов и текущую температуру газовой смеси: x1 = Gv; x2 = t , то операторная схема будет соответствовать рисунку 3. На рисунке основными обозначениями в схеме являются:
а) нумерация блоков в порядке возрастания — используемые в установке аппараты – реактор термического разложения, скруббер, газовый холодильник, абсорбер селективного поглощения (два последовательных аппарата), хвостовой адсорбер;
б) управление потоками осуществляется через подогрев, охлаждение, парообразование, шлаковыделение в зависимости от технологического предназначения аппарата.
Разработка технологической схемы установки по очистке отходящих газов при термическом обезвреживании пестицидов предусматривает главное условие – реактор термического разложения основан на естественном конвективном притоке воздуха в зону реакции. Поэтому необходимо выбрать способ создания движущей силы, приводящей к перемещению газов через аппараты установки.
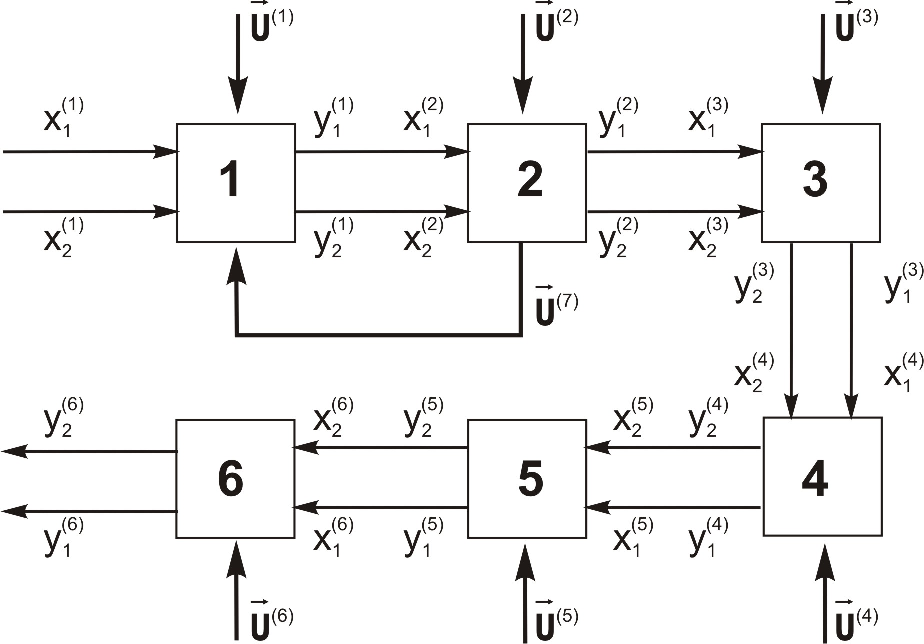
Наиболее оптимальным решением по созданию движущей силы для перемещения отходящих газов является использование струйного компрессора, размещаемого непосредственно за реактором термического разложения. Данное технологическое решение обусловлено несколькими обстоятельствами.
Во-первых, горячие отходящие газы перемешиваются со свежим холодным воздухом, понижая собственную температуру, что приводит к начальным условиям создания закалки газов.
Во-вторых, появляется возможность регулировать поток газовой смеси, создавая требуемую движущую силу для всей лабораторной установки.
В-третьих, в камере реактора термического разложения сохраняется конвективный поток и температурные параметры в зоне реакции не меняются, так как отходящие газы удаляются за счет инжекции в камере смешения струйного компрессора.
В-четвертых, введение избыточного количества воздуха в поток отходящих газов обусловливает превращение образовавшейся в реакторе окиси углерода в двуокись.
И, наконец, в-пятых, при смешении отходящих газов со свежим воздухом происходит снижение концентраций вредных примесей, что влияет на повышение степени извлечения веществ при применении массообменных процессов.
Далее поток отходящих газов направляется в скруббер, где происходит закалка газов, очистка от твердых частиц дыма и удаление окислов азота. После чего газы перемещаются в теплообменник для дальнейшего снижения температуры и отделения от смеси конденсата. Охлажденные газы направляются на абсорберы селективного поглощения и после дополнительного удаления водяного конденсата проходят адсорбер и сбрасываются в атмосферу. Предлагаемая технологическая схема представлена на рисунке 4 .
1- скруббер отходящих газов; 2- абсорберы селективного поглощения; 3- адсорбер; 4- кожухотрубчатый теплообменник, 4а- отделитель конденсата; 5- аппарат приготовления рабочих растворов; 6- расходные емкости; 7- приемные емкости; 8- струйный компрессор; 9- конденсатоотводчики
Рисунок 4 – Технологическая схема установки по очистке отходящих газов при термическом обезвреживании пестицидов
Отходящие газы при температуре 1200 0С по соединительному патрубку принудительно поступают в струйный компрессор 8, где смешиваясь со сжатым воздухом из линии компрессора, понижают температуру до 650 0С на срезе струйного компрессора. Линия компрессора запитывается сжатым воздухом с давлением 0,25 МПа. Производительность струйного компрессора обеспечивается регулировочным вентилем на линии и подачей регулировочного сопла на самом струйном компрессоре.
Смесь газов поступает в полый скруббер 1, где происходит закалка газов и понижение температуры смеси до 200 – 250 0С. Скруббер снаряжается металлической стружкой и орошается раствором карбамата из расходной емкости 6. Излишек жидкости собирается в нижней части аппарата и выводится в приемную емкость 7, откуда, по мере накопления, эрлифтом передавливается обратно в расходную емкость 6.
Очищенная от твердых частиц смесь газов поступает в кожухотрубчатый холодильник 4 и через конденсатотводчик 9 направляется в насадочный абсорбер 2 при температуре 20 – 25 0С. Абсорбционные колонны 2 орошаются водным раствором соответствующей соли из расходной емкости 6, для достижения хемосорбционного эффекта с целью получения технических минеральных продуктов. Абсорбент собирается в приемных емкостях 7, откуда, по мере накопления, эрлифтом передавливается обратно в расходные емкости 6.
В системе газоочистки отходящих газов предусматривается двухступенчатое поглощение абсорбтива с целью максимального выделения примеси из газовой смеси. Первая и вторая ступени очистки отходящих газов идентичны между собой в аппаратурном и технологическом оформлении.
По выходу из хвостового абсорбера газы попадают на отделитель конденсата 4а и конденсатотводчик 9 для выделения избыточной влаги, после чего поступают в адсорбер и сбрасываются в атмосферу.
В технологической линии очистки отходящих газов предусмотрен узел приготовления растворов соответствующих солей для орошения в колонных аппаратах. Узел приготовления растворов представляет собой мерную емкость 5 с пропеллерной мешалкой и системой слива в соответствующие расходные емкости.
Приемные емкости 7 по мере израсходования действующих веществ, что определяется аналитически, опорожняются на слив и в соответствии с технологическим регламентом либо концентрируются для получения целевого продукта, либо концентрируются для направления на сжигание в термическую печь.
В технологическом процессе используется вода оборотная для съема тепловой нагрузки на теплообменниках и приготовления рабочих растворов. Сжатый воздух используется для создания движущей силы газовому потоку, для создания давления жидкости при орошении колонных аппаратов и для обеспечения эрлифта в приемных емкостях.
При технологическом функционировании установки образуются следующие типы отходов:
- шлаковые массы из реактора термического разложения состава, представляющего собой смеси углерода в виде сажи, оксидов и сульфидов металлов, пековых масс наполнителей препаративных форм пестицидов;
- шлам из скруббера, представляющего собой смесь углерода в виде сажи, нитратов и нитритов аммония, калия или кальция (что определяет собой выбранный раствор для орошения скруббера);
- отработанные водные растворы из абсорберов селективного поглощения, собирающиеся в приемных емкостях;
- отработанный адсорбент из хвостового адсорбера.
Уровень опасности представленных отходов не превышает 4 – 5 класс опасности по действующим в Российской Федерации нормативным классификаторам.
Предполагается применять следующие основные способы утилизации отходов, образующихся при функционировании установки по термическому разложению пестицидов:
- шлаковые массы, образующиеся в реакторе термического разложения, предлагается использовать в качестве наполнителей для асфальтовых масс и наполнителей для строительных материалов;
- шлам из скруббера необходимо загружать в отстойники для отбора осветленной части в качестве товарного продукта. Загущенная часть, предварительно досушенная с использованием утилизированного тепла реактора термического разложения, перемещается в голову процесса на смешение с исходной формой пестицида для повторного разложения;
- отработанные водные растворы из абсорберов должны представлять собой товарные формы растворов удобрений для нужд агропромышленного комплекса.
- отработанный адсорбент из хвостового адсорбера требуется регенерировать острым паром, досушивать и повторно использовать в аппарате.
Выводы
- Обоснован перечень газообразных продуктов горения в отходящих газах при термическом разложении пестицидов различных классов.
- Составлен теоретический материальный баланс процесса высокотемпературной деструкции пестицидов на основе закона сохранения массы и определены его статьи, позволяющие выявить параметры установки для термического разложения пестицидов и разработать технологическую схему очистки отходящих газов. Статьи баланса подтверждают соответствие поступающей и обрабатывающейся при проведении процесса массы веществ.
- Определены значения величин экспериментальных данных по количественному и качественному составу отходящих газов, образующихся при термическом обезвреживании модельных образцов пестицидов, и показано, что в условиях эксперимента качественный состав газообразных продуктов горения соответствует аналогичным результатам теоретических исследований. При этом диоксиноподобные соединения не обнаружены.
- Проведен расчет материального баланса процесса термического разложения модельного образца и установлено, что количественное содержание газообразных продуктов горения в отходящих газах в соответствии с теоретическим и экспериментальным материальными балансами не совпадает. Расхождение содержания (массовых долей) загрязнителей отходящих газов составляет от 9,6 до 120,5 % и зависит от типа загрязнителя.
- Разработана технологическая схема лабораторной установки для термического обезвреживания пестицидов и отходящих газов.
Список литературы
- Ашихмина Т.Я. Экологический мониторинг. Киров: Константа, 2005. 414 с.
- Ларионов К.В. Разработка плазменно-пиролитического способа утилизации непригодных к применению пестицидов. Автореф. дисс. … к.т.н. Краснодар: Кубанский ГУ, 2009. 17 с.
- Петрук В.Г., Яворская О.Г., Васильковский И.В. Современные экологически безопасные технологии обезвреживания непригодных пестицидов / Под ред. Петрука В.Г. Винница: “Универсум-Винница”, 2003. 253 с.
- Петрук В. Г. Экологические аспекты термического уничтожения непригодных агрохимикатов. Винница: “Универсум-Винница”, 2005. 261 с.
- Повякель Л.И., Кривенчук В.Е., Любинская Л.А. Анализ остаточного пепла, как вторичного отхода после уничтожения непригодных и запрещенных пестицидов методом пиролиза // Сборник докладов на НТК «Сбор и утилизация отходов» Института экогигиены и токсикологии им. Медведя. Киев, 2002.
- Буков Н.Н., Ларионов К.В. Утилизация хлорсодержащих пестицидов // Экология и промышленность России. 2007. № 3.
- Буков Н.Н., Ларионов К.В., Репная Л.Ф. и др. Утилизация некоторых препаративных форм некондиционных хлорорганических пестицидов //Известия ВУЗов. Северо-Кавказский регион. Естественные науки. 2005. № 7.
- Репная Л.Ф., Буков Н.Н., Панюшкин В.Т. и др. Исследование процессов пиролитического разложения некоторых классов пестицидов //Известия ВУЗов. Северо-Кавказский регион. Естественные науки. 2004. № 12.
- Петрук В.Г., Скоробогач И.Л. Термическое обезвреживание фосфорсодержащих пестицидных препаратов в восстановительной среде //Науковi працi ВНТУ. 2008. № 7.
- Хитрин Л.Н. Физика горения и взрыва. М.:Московский ГУ, 1957. 442 с.
- Касаткин А.Г. Основные процессы и аппараты химической технологии. М.:Химия, 1973. 750 с.
- Кутепов А.М. Общая химическая технология. М.:ИКЦ «Академкнига», 2003. 546 с.
- Методы и средства автоматизированного расчета ХТС. Л.:Химия, 1987. 152 с.
- Оборудование, сооружения, основы проектирования химико-технологических процессов защиты биосферы от промышленных выбросов. М.:Химия, 1985. 345 с.
- Мухленов И.П. Расчеты химико-технологических процессов. Л.:Химия, 1982. 248 с.